Storm Water Management Services
Salient Solutions administers the requirements of local, state, and federal Storm Water Management (SWM) guidelines. These are regulated by the local county agencies of the Department of Public Works and Transportation (DPWT), Department of Permitting, Inspections, and Enforcement (DPIE), Maryland Department of the Environment (MDE), and the Environmental Protection Agency (EPA). We provide systematic site monitoring of all regulatory standards for the Storm Water Pollution Prevention Program (SWPPP). This includes their mandatory inspection reports under the General Permit for National Pollutant Discharge Elimination Systems (NPDES).
The conversion of interim Storm Water Management ponds and sediment traps and their Best Management Practices (BMP) is a Salient Solutions specialty. In the last 42 conversion projects, the Salient Solutions team accomplished on-site disposals of all sediment loaded soils ranging from 500 CY to 3,500 CY of useless soils. These management protocols eliminated the remarkably expensive cost of exporting to off-site locations. This saved our clients more than $630k.
Two of our permanent SWM pond conversions challenged Salient Solutions to provide 24/7 active stream flows during the entire reclamation project. These procedures were monitored by the United States Army Corps of Engineers (USACE) and MDE to certify protection of the existing upstream wetlands
Our Storm Water Management Projects Include:
The land development sequence begins with the following: clear only the perimeter Limits Of Disturbance (LOD) and sediment trap locations, install LOD fencing and silt fence enclosures, construct sediment traps and SWM ponds with their structures and controls per approved grading plans, request county initial inspections, and when approved, authorization allows for the clearing, grubbing, and mass grading for up to 20 acres of disturbance for the development to begin.
Sediment controls require weekly inspections, an inspection within 24 hours of each rain event seven days a week including holidays. Each inspection is memorialized in a four-page MDE reporting format documenting the exact status of the development site at the time of the inspection. These reports must be produced to MDE within one hour of notification. This can include the entire inspection history. After Notice of Termination is submitted and approved by MDE, all written reports must be maintained for a 3 year period. Non compliance is subject to civil/criminal penalties.
Salient Solutions provides these Storm Water Pollution Prevention Program (SWPPP) inspection services and reports. We represents the permittee at all county, MDE or EPA field audits.
Cheltenham Park with 2 Permanent SWM Ponds and 1 Sediment Trap
CHALLENGES: Salient Solutions developed plan modifications to provide for the onsite disposal of 50,000 CY’s of surplus soils. This saved $750K. We identified on-site disposal of 3,200 CY’s of SWM pond sediment-laden soils saving the cost for offsite disposal. This resulted in $80K in cost savings. Stephen Gunn negotiated an additional cost savings of $493K for reduced right-of-way improvements with his detailed management records and onsite testing,
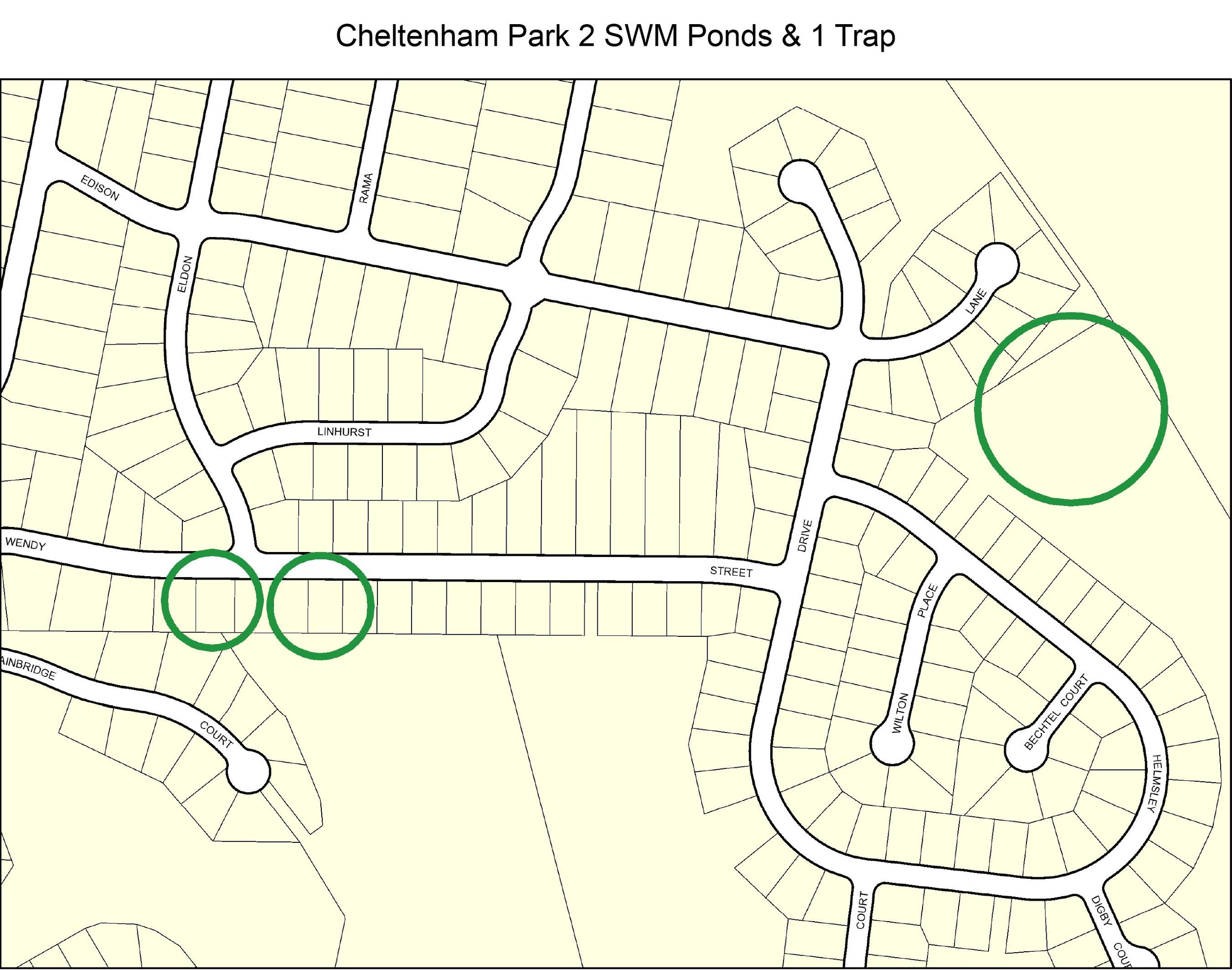
Equestrian Estates with 2 In-Stream SWM Ponds and 8 Sediment Traps
CHALLENGES: Salient Solutions inherited a county citation that ordered the removal of 116,000 CY’s of non-useable surplus site soils which had been placed in five non-approved stockpile locations. The resolution saved $1.16 million. We inherited a shortfall of 35,000 CY’s of structural fill materials. These materials were required to close six remaining sediment traps to complete the mass site grading in Phases 1B and 2. Even though we had forty vertical feet of fill placements, our creative resolution saved $350K for the developer. Last, we inherited an approved Site Plan with a hiker/biker trail system designed within a flood plain and requiring five structural bridges to cross active streams. Salient Solutions saved $270K by redesigning the plan for an environmentally friendly user experience.
BEFORE CONVERSION:

DURING CONVERSION:
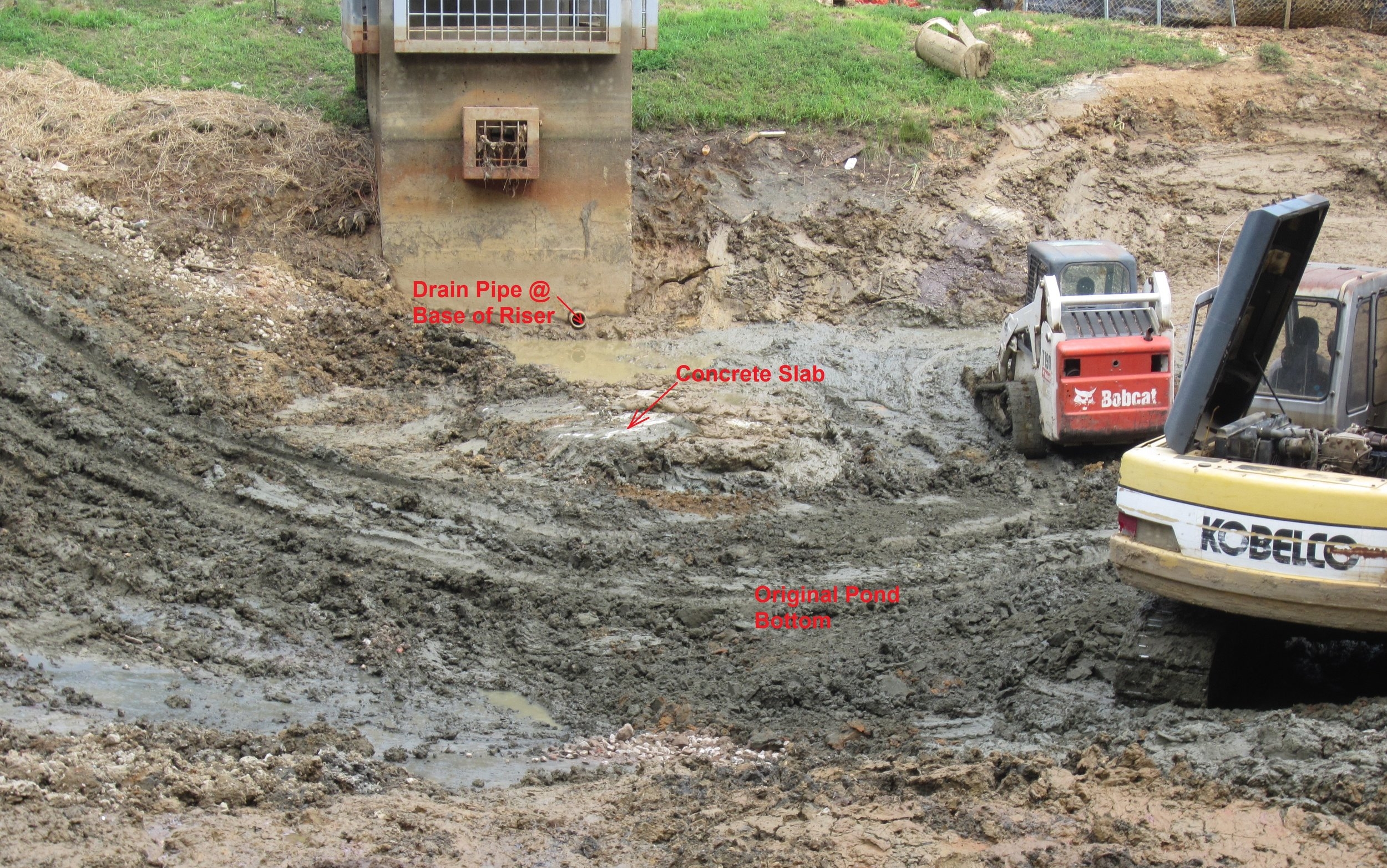
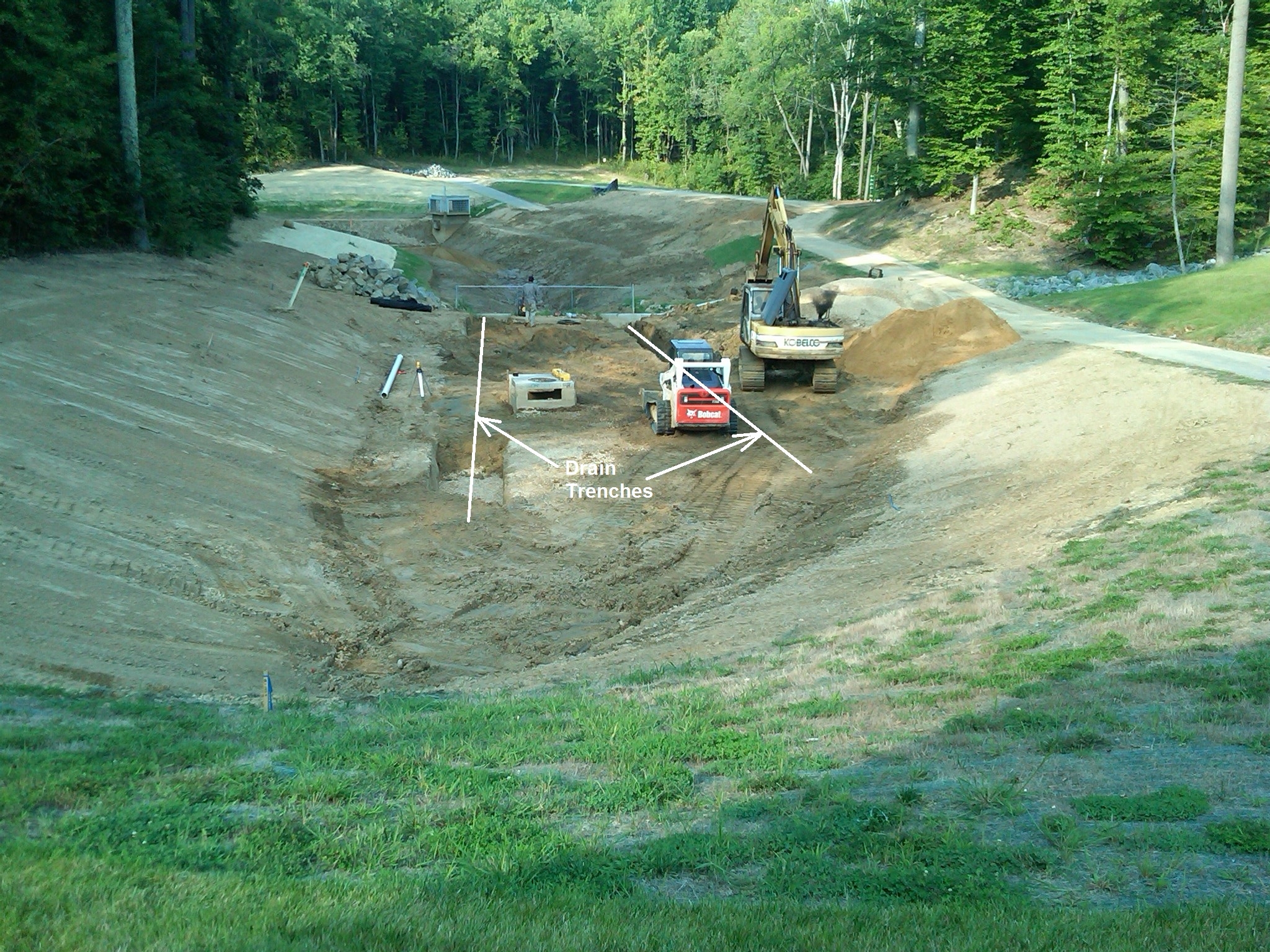
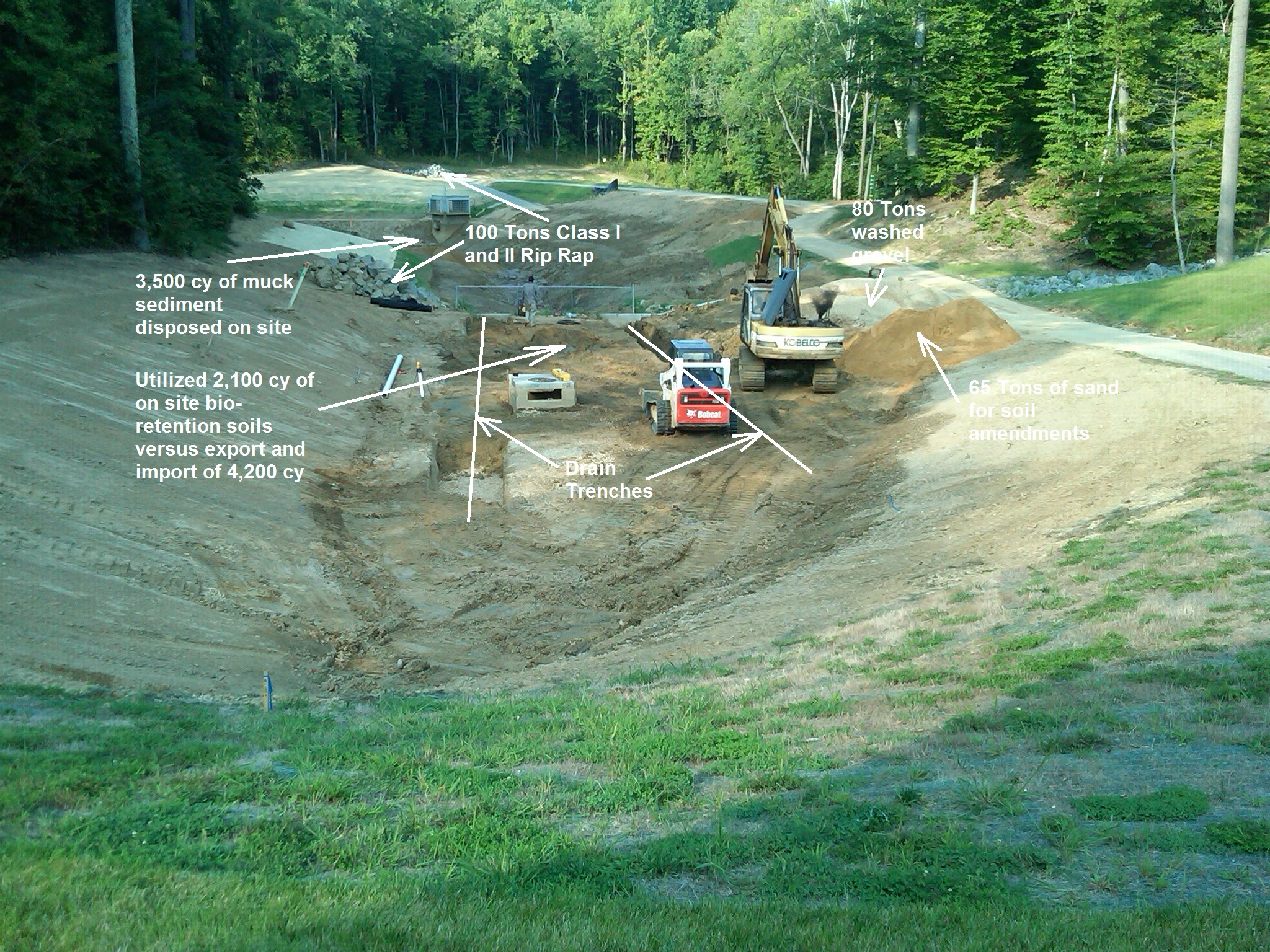
AFTER CONVERSION:
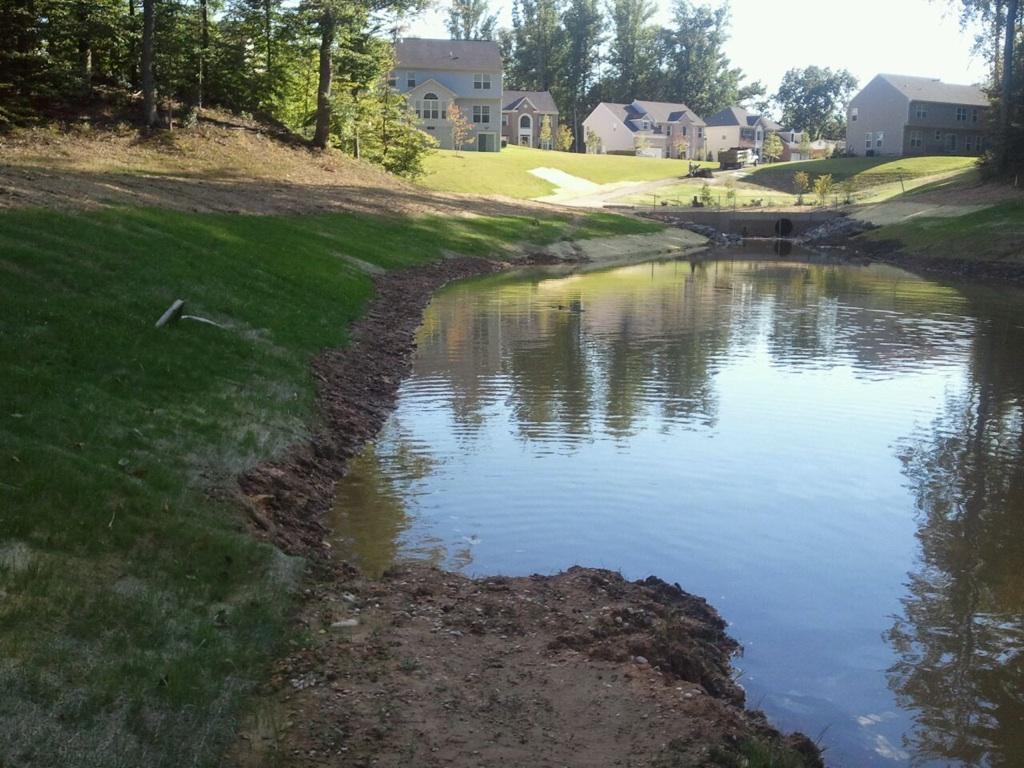
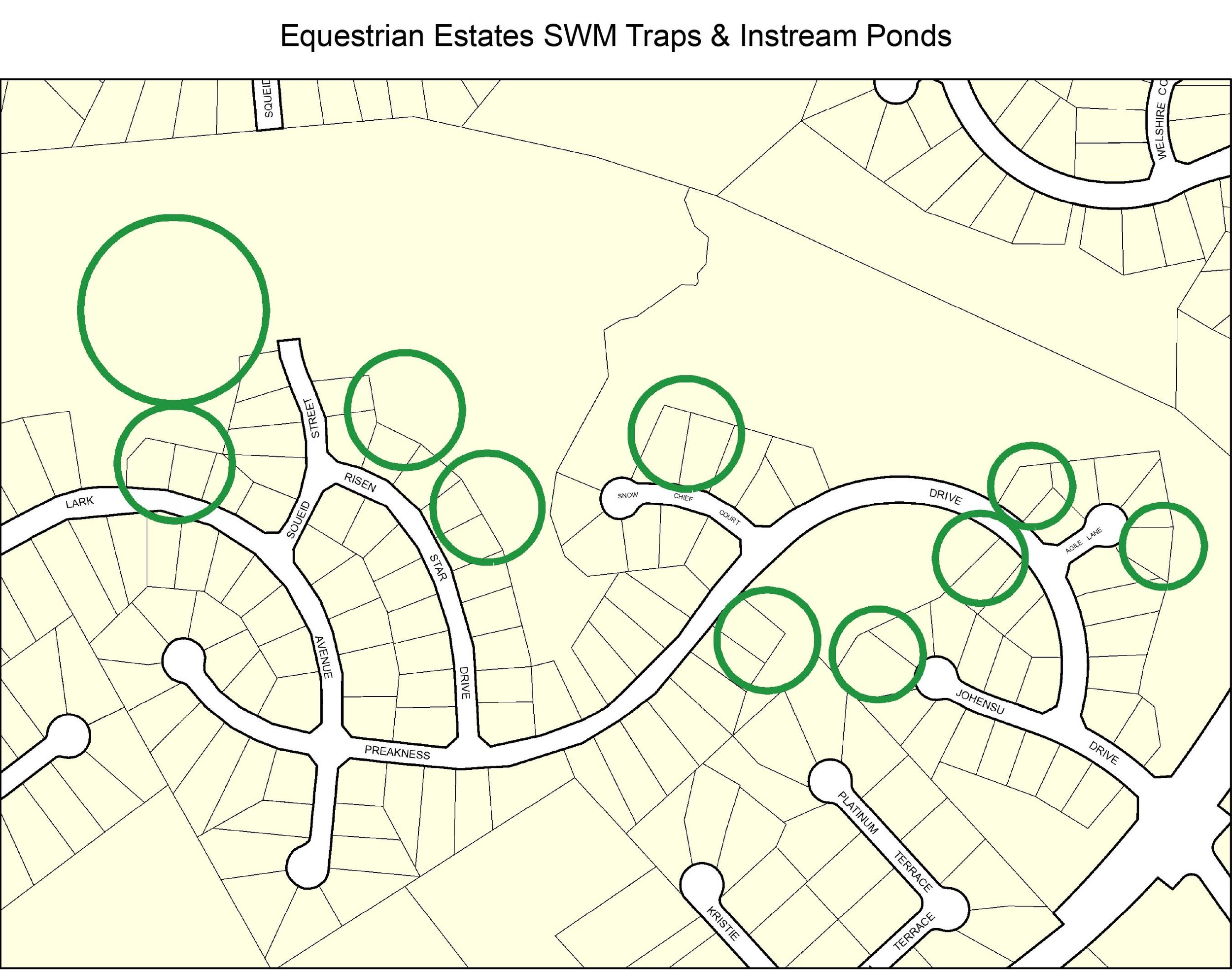
Windsong with 2 Permanent SWM Ponds and 2 Sediment Traps
CHALLENGES: The challenges Salient Solutions faced were formidable. There was major road paving corrective work. The SWM pond conversions were daunting after 10 years of neglect and two sediment traps were mandated to be closed. The engineering certifications for a $500K defaulted bond completion project had time constraints with penalty provisions of $126K.
BEFORE CONVERSION:
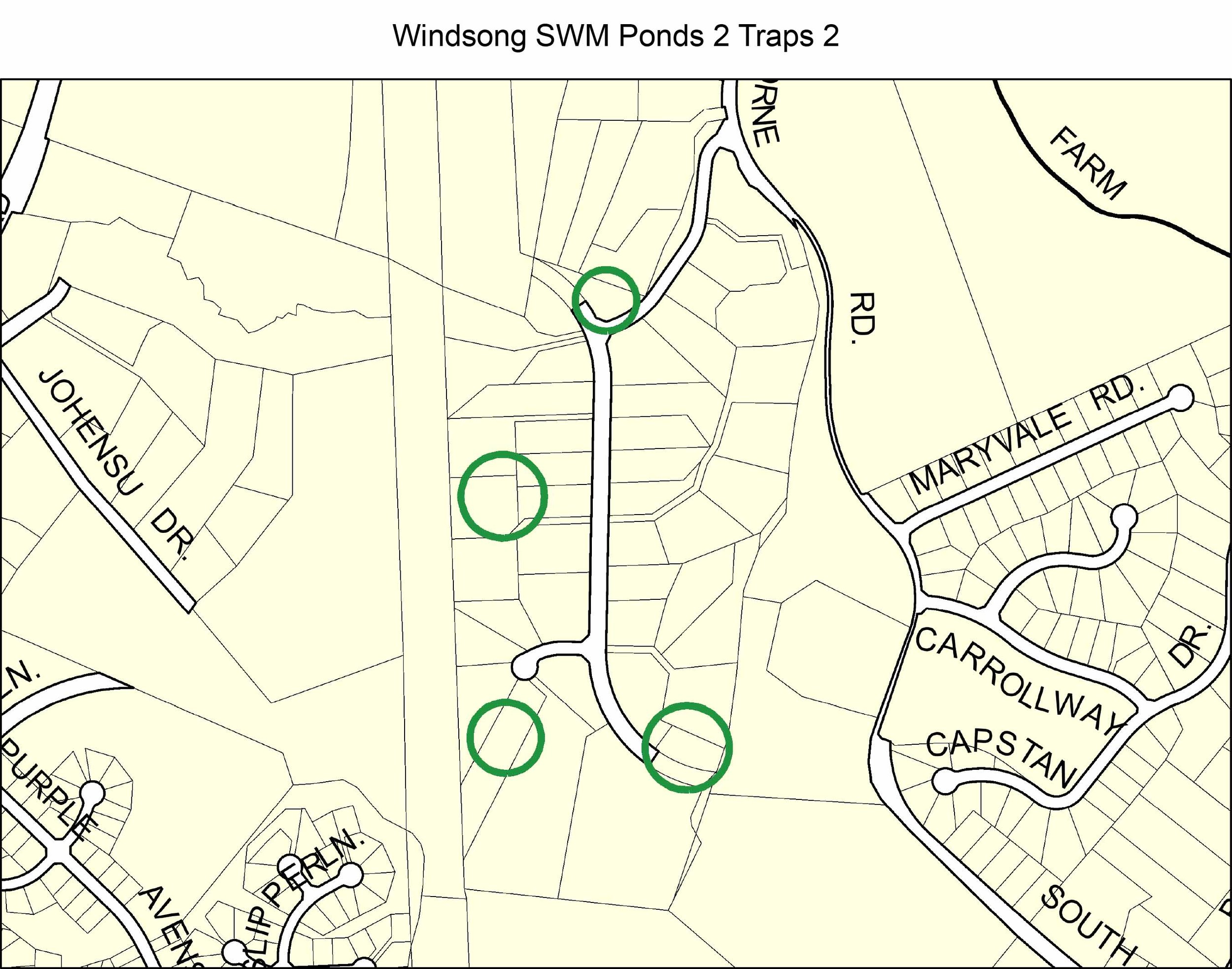
DURING CONVERSION:
AFTER CONVERSION:
Piscataway Landing Phases 1, 2, 3 and 7 Sediment Traps
CHALLENGES: Salient Solutions inherited an approved site plan resulting in a dirt shortfall of 125,000 CY’s in Phases 2 and 3 . Stephen Gunn located free dirt/delivery saving $1.3 million in imported costs. Seven sediment traps contained an average of 500 CY’s of muck. This was disposed of onsite for a savings of $87.5K. The sediment trap on Lot 16B required 40 vertical feet of structural fill materials to bring the lot to grade for house-line construction. Phase 3 contained an average of 3.5 to 4.0 vertical feet of mud. This contained more than 40,000 CY’s of non-fill materials that required temporary drainage systems and drying in order to proceed.
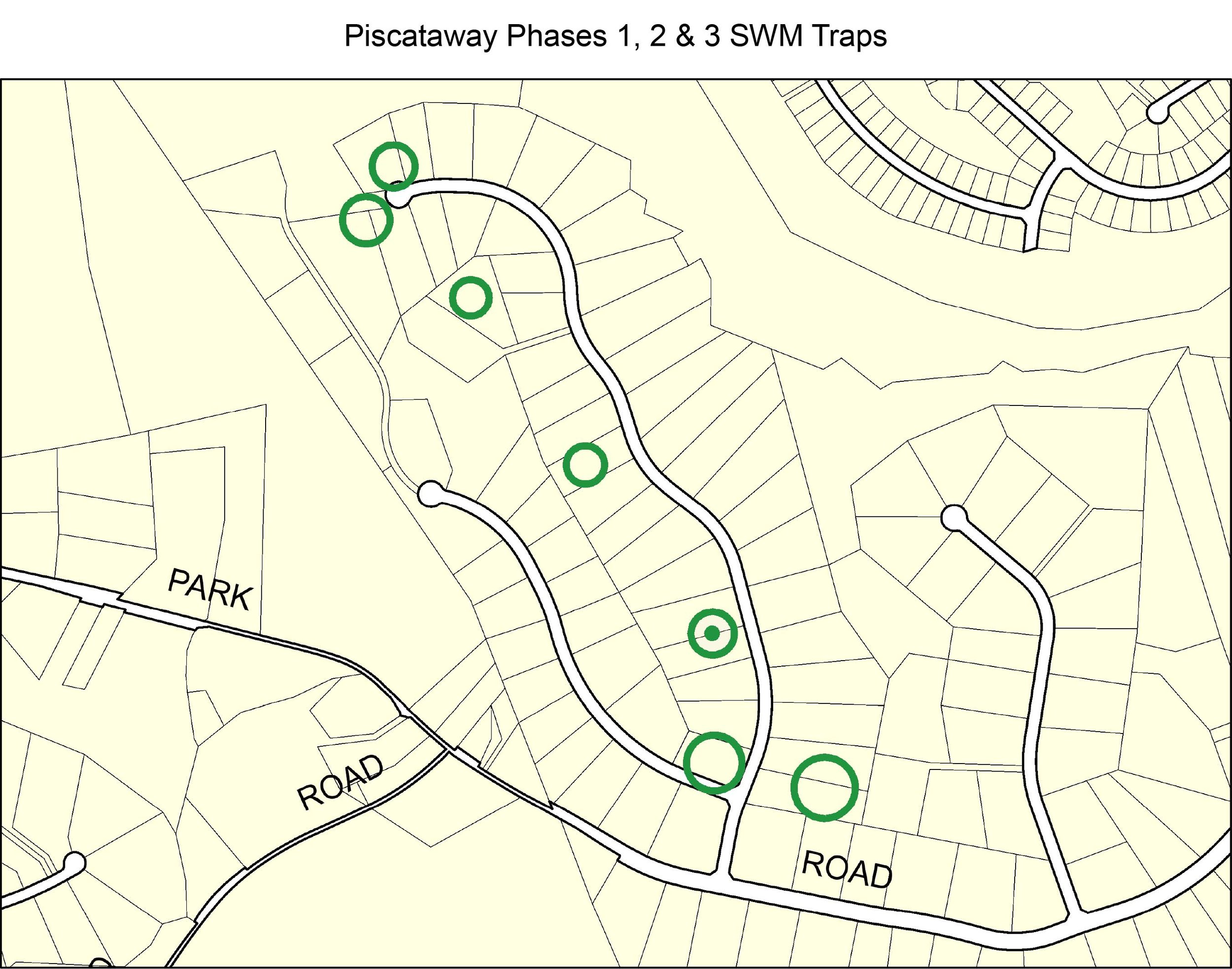
Fairview Manor & Collingbrook Estates 4 Sediment Traps in First 2 Phases
CHALLENGES: All site development contracts for Fairview Manor had been awarded prior to Salient Solutions being retained by Caruso Homes and they were behind schedule. Salient Solutions directed four revisions to the TCP-II Tree Conservation Plans that resulted in cost reductions of $366K for phases 1, 2 and 3. The Storm Drain & Paving plans were revised and in place contracts were re-negotiated. Five new contractors/suppliers were substituted for those who were originally in place resulting in cost reductions of $360K. The Sediment Trap conversions succeeded in the disposal of mud and sediment to onsite locations reducing costs to export. Salient Solutions caused the Waste Water Pumping Station (WWPS) to achieve a predictable schedule and delivered the facility with all approvals in April 2016.
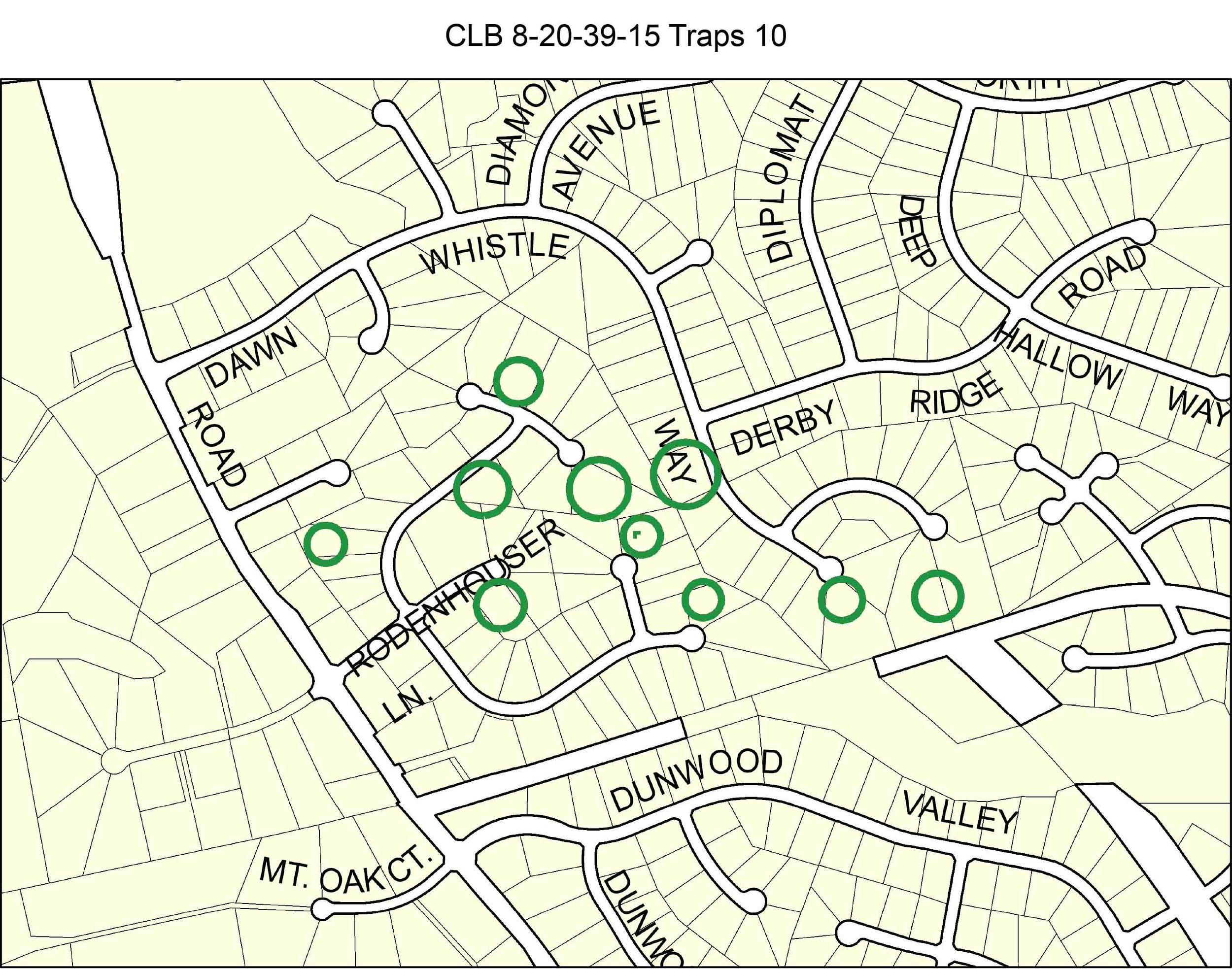
The Overlook at Hunter Mill 1 Permanent SWM Pond, 3 Sediment Traps
CHALLENGES: Salient Solutions inherited a development site that was 100% active in 2006-2007. It subsequently defaulted and restarted in 2016. The approved plans showed a dirt surplus of 38,000 CY’s over the 30-acre site which would have resulted in a removal cost of $570K. Salient Solutions recommended the engineer revise the entire grading plan to balance the site. The original sewer and storm drain structures were delivered to the site in 2006 and remain there to this day. Salient Solutions located and certified these 10-year old materials and saved the developer $80K. Salient Solutions inherited two stockpiles of 8,000 CY’s and 10,000 CY’s. These were composed of topsoil and organic materials which restricted their use and applications. Stephen Gunn secured a waiver of county required underdrains that resulted in a cost reduction of $115K and went on to negotiate and secure an out-of-state specialty contractor resulting in a cost reduction of $30K for Phase 1B.
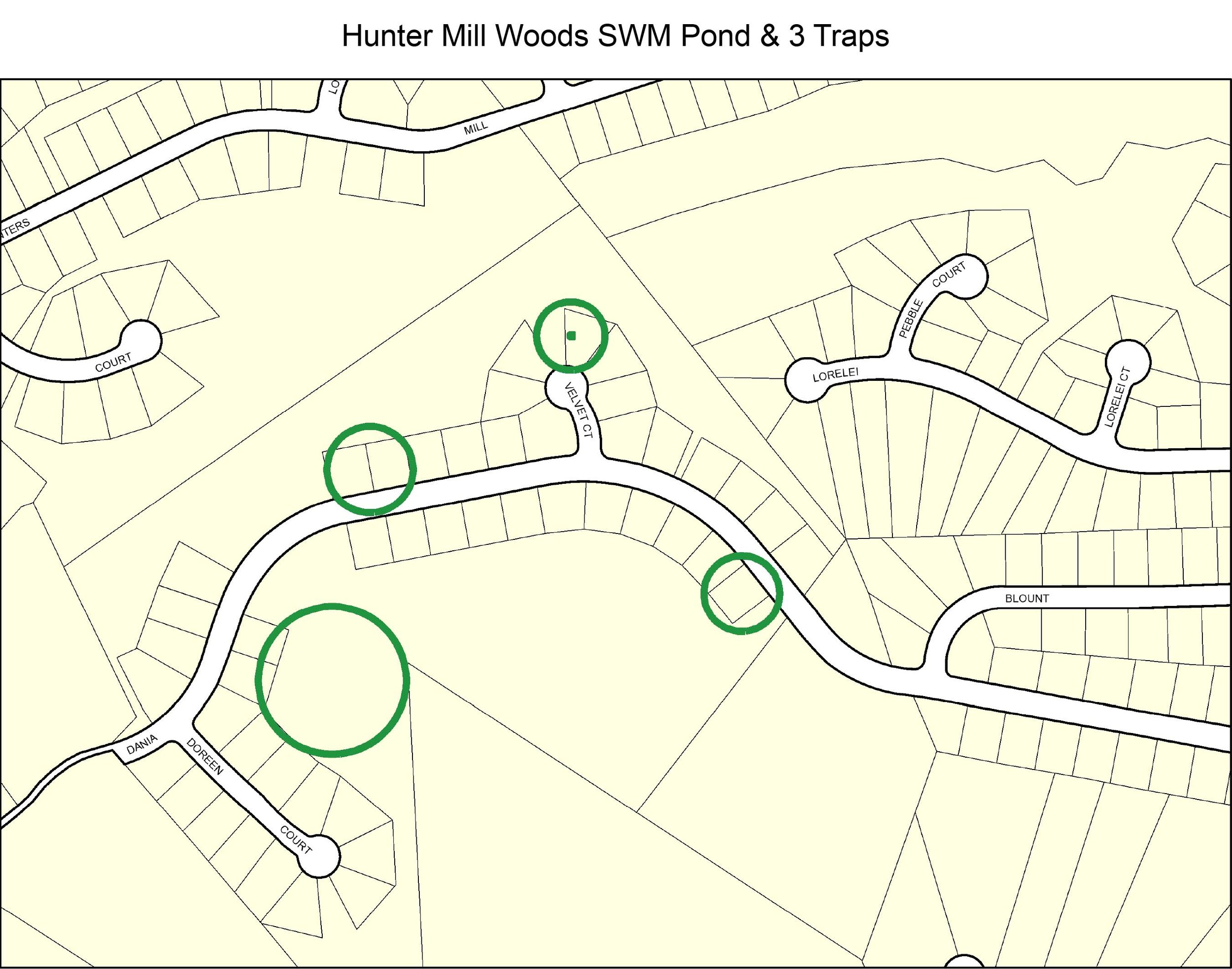
Westphalia ROW with 1 Permanent SWM Pond and 2 Sediment Traps
CHALLENGES: Market introduction delays resulted in the selling of two phases to public home building companies resulting in winter season development restrictions. Structural fill shortages for Phase 2 and 3 required the importing of 30,000 CY’s of materials between June and November of 2014. Stephen Gunn negotiated free resources of dirt and delivery resulting in a cost savings of $195K. Gunn directed the geotechnical reports to be revised to eliminate the county requirement of underdrains in Phase 1D and 2 resulting in a cost savings of $81K. He managed a major environmental spill that required two environmental reviews and 1,076.48 tons of contaminated materials to be removed from the site and replaced with new structural materials. Gunn recruited a competitor’s sales manager which resulted in him joining Haverford Homes where he jump started the successful marketing of the community which enabled the developer to reserve the remaining 205 lots for Haverford Homes.
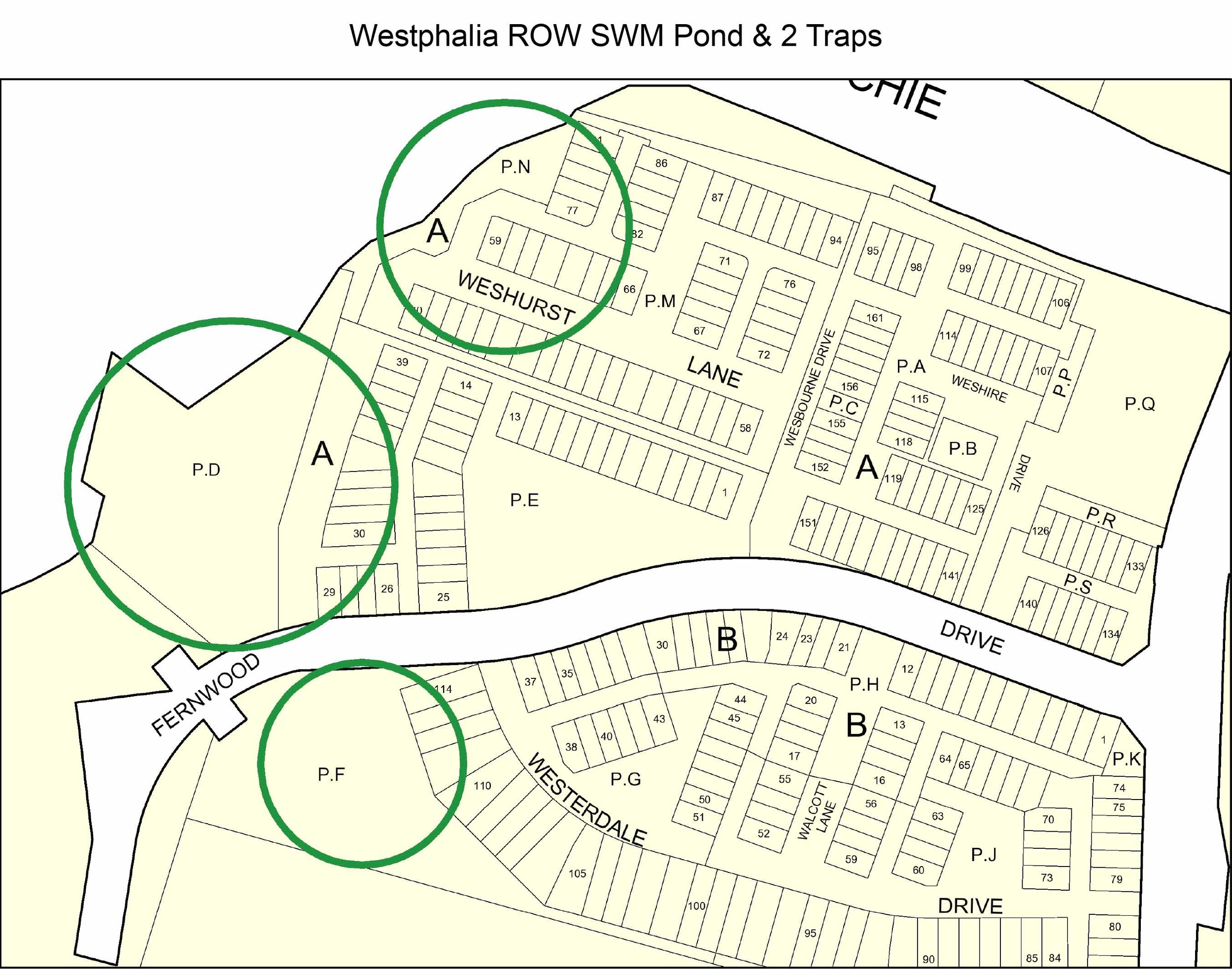
St. James Phase 1 & 2 with 2 Permanent SWM Ponds 7 Sediment Traps
CHALLENGES: Stephen Gunn joined Haverford Homes as Director of Land Development in the Spring of 2007. The first phase of St. James improvements began in 2005 and continued in 2006. He discovered substantial dirt shortages, reforestation violations, Storm Water Management (SWM) maintenance infractions, and access road issues from the Livingston Road public right-of-way into both Phase 1 and Phase 2. Gunn discovered that a portion along the northern section of the St. James property was being farmed by an adjacent property owner for the past 25 years. Once discovered, the land was restored back to St. James. Phase 1 had a dirt shortfall of 20,000 CY’s which would have resulted in an import cost of between $250K - $300K. Gunn acquired free dirt resources to make up this difference.
Phase 2 was delayed due to market conditions and major design requirements for offsite improvements. These included a 4-lane intersection and road frontage, power and communication transmission pole relocation, Marlboro clay soil conditions requiring extensive geotechnical redesign for compliance, major earthwork adjustments to balance cut and fills, 92,084 CY’s of surplus soils, and three major stream crossings estimated at $550K. Phase 2A began under Gunn’s management with the first 18 estate lots, three sediment traps, and the triple box culvert system at the entrance.
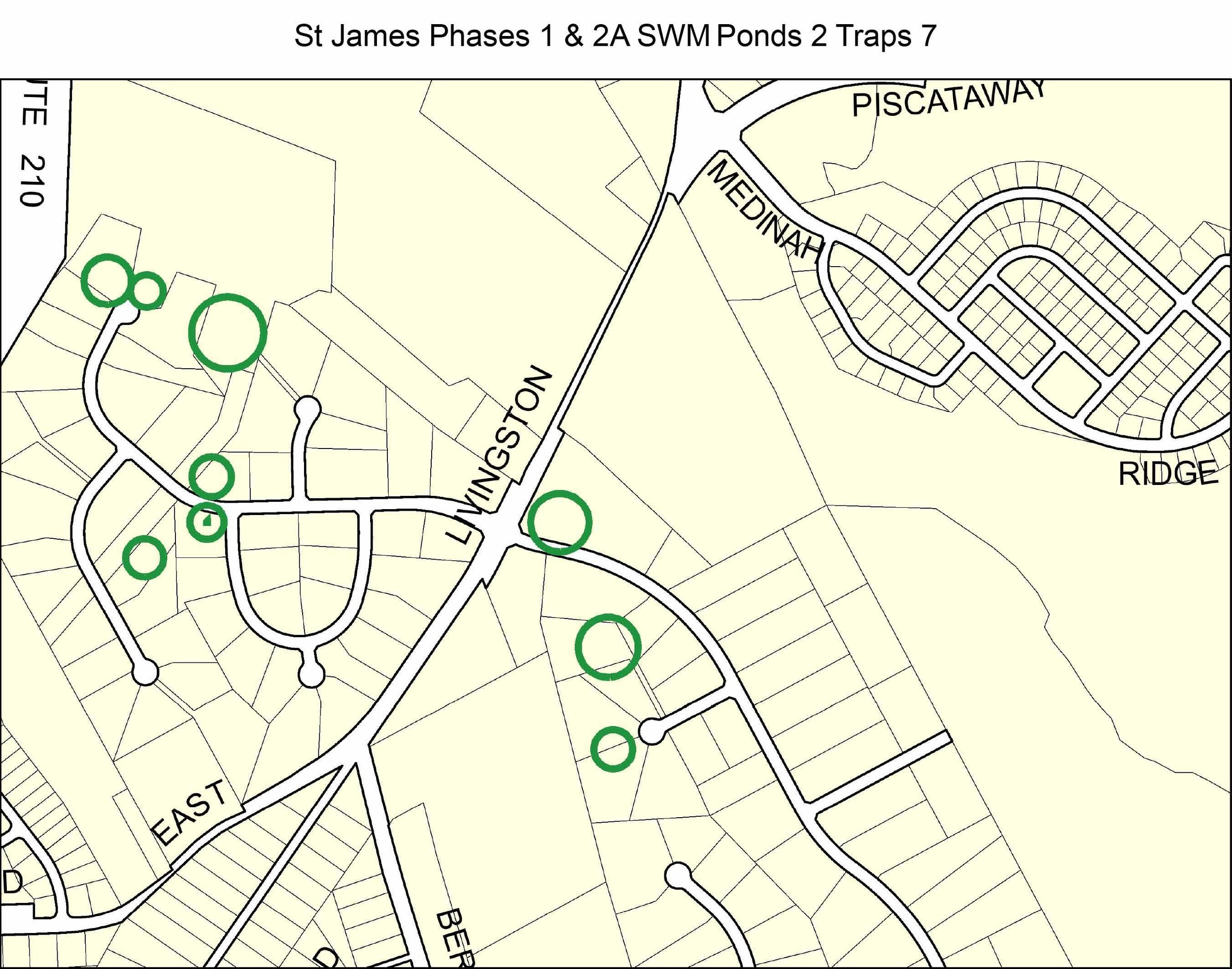
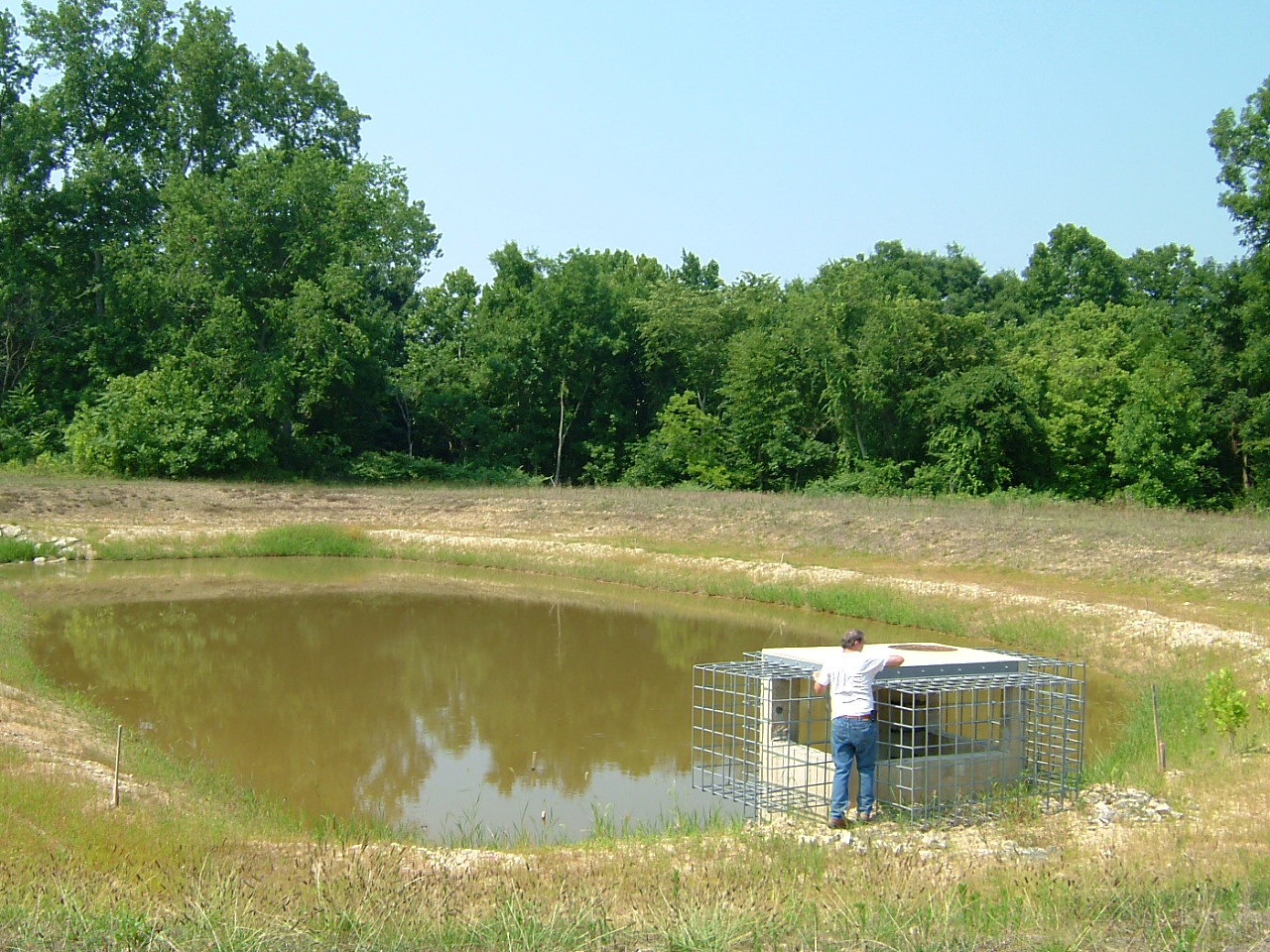
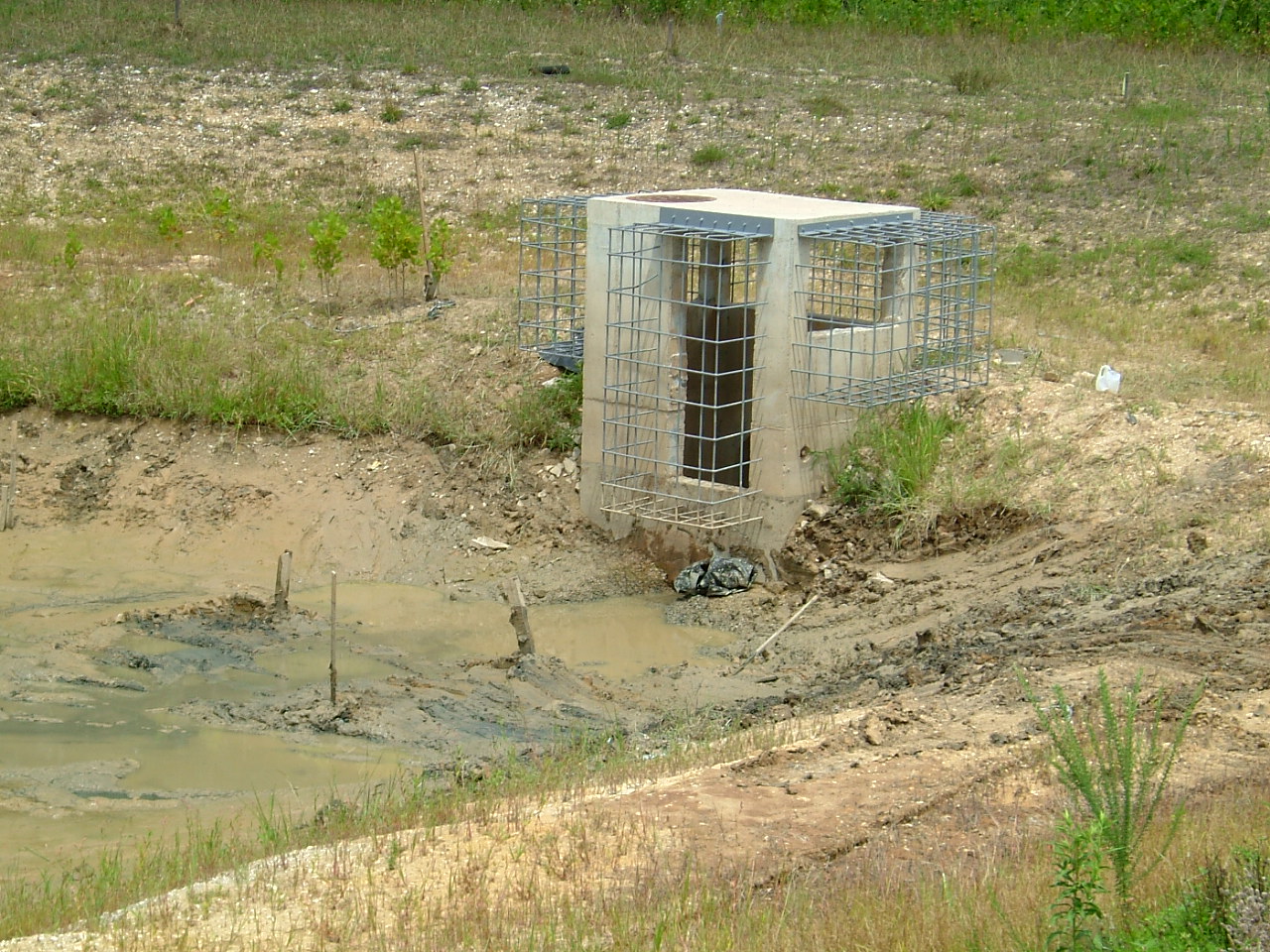
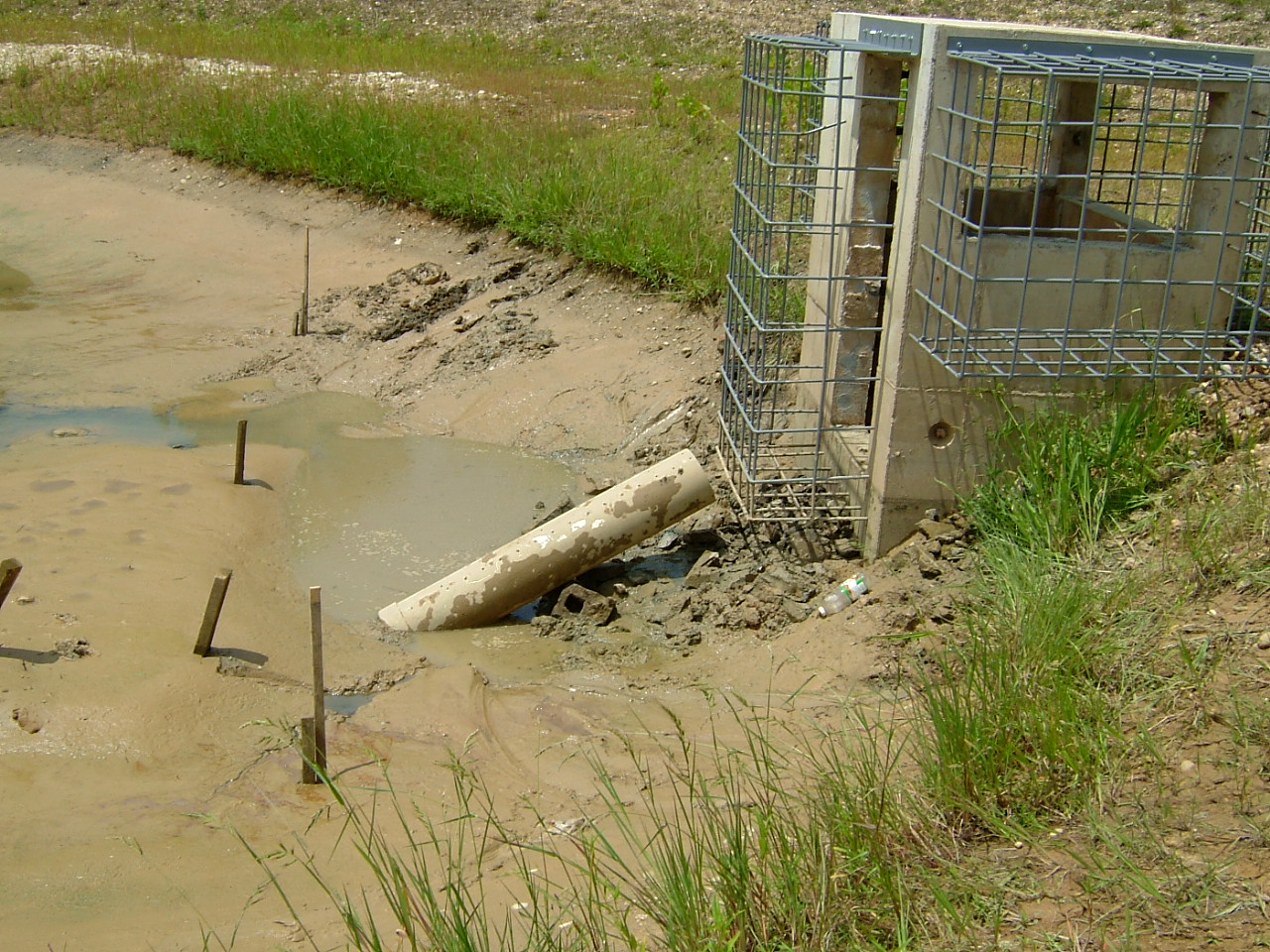